previous Principles of Pyrolysis and Gasification
6. Examples of Waste Pyrolysis
6.1 Biomass
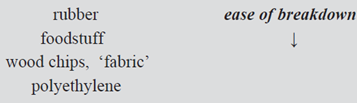
*Abbreviations for the respective polymers given in row 1 retained.

6. Examples of Waste Pyrolysis
6.1 Biomass
When wood decomposes it releases a miscellany of simple organic compounds. Many centuries ago, perhaps even in the pre-Christian era, the breakdown products of wood found application, for example as what later came to be called antiseptics. It is sometimes asserted that this is the oldest example of ‘applied chemistry’, ‘chemical technology’ or whatever. The gist of the previous chapter was such that the essentials of biomass pyrolysis were brought out. At the present time there is major interest in copyrolysis of biomass with substances including plastics. In this chapter a discussion of such co-pyrolysis will follow coverage of pyrolysis of two very important types of waste: MSW and plastic waste.
6.2 Municipal solid waste
MSW combustion, in raw and pelletised form, was the subject of three previous chapters. Discussion of its pyrolysis was deferred until background on the pyrolytic processes generally had been given. There has been and is much interest in the pyrolysis of MSW and that will be the subject of this section.
Attempts to make useful products from pyrolysis of MSW are by no means new. An account of pyrolysis on a trial basis of ‘municipal garbage’ features in a monograph from 35 years ago [1]([1] Bell P.R., Varjavandi J.J. ‘Pyrolysis – Resource Recovery from Solid Waste’ Waste Management, Control, Recovery and Re-use’ (N.Y. Kirov, Ed.) Ann Arbor Science (1975)), nor was that the first such investigation to be reported. The table below gives selected examples of pyrolysis of MSW. The examples in the table range from laboratory scale to full, commercially operating scale. Comments follow the table.
Reference
|
Details
|
[1]
|
Pyrolysis temperatures in the range 500 to 900°C. Per tonne of raw MSW, up to 200 kg of char, up to 15 litres of oil and up to 500 m3 of flammable gas.
|
[2] Jiao Z., Yu-qi J., Yong C., Jun-ming W., Xu-guang J., Ming-jiang N. ‘Pyrolysis characteristics of organic components of MSW at high heating rates’ Waste Management 29 1089-1094 (2009)
|
Pyrolysis of laboratory size samples of rubber, paper, wood chips, ‘fabric’, foodstuff and polyethylene, simulating the separate components of MSW. Respective reactivities to decomposition investigated by thermal analysis.
|
[3] Islam M.N., Beg M.R., Islam M.R. ‘Pyrolytic oil from fixed bed pyrolysis of MSW and its characterisation’ Renewable Energy 30 413-420 (2005)
|
Pyrolysis of the paper component only of MSW at 450°C, directed at oil as the primary product.
|
[4] http://www.splainex.com/waste_recycling.htm |
MSW pyrolysis with combustion of the products for generation of electricity most of which is sold to the grid.
|
[5] Korkmaz A., Yanik J., Brebu M., Vasile C. ‘Pyrolysis of the Tetra Pak’ Waste Management 29 2836-2841 (2009)
|
Pyrolysis of Tetra Pak [6]([6] http://www.tetrapak.com/products_and_services/Pages/default.aspx) products. A considerable amount of wax in the pyrolysate.
|
[7] Buah W.K., Cunliffe A.M., Williams P.T. ‘Characterisation of the products from the pyrolysis of municipal solid waste’ Transactions of the Institution of Chemical Engineers Part B Process Safety and Environmental Protection 85 450-457 (2007)
|
Laboratory study of the pyrolysis of RDF pellets. Pyrolysis temperatures up to 700°C.
|
[8] Gupta B., Shepherd P. ‘Data Summary of Municipal Solid Waste Management Alternatives’ NREL, Golden CO (1992)
|
Funabashi City, Japan (part of Greater Tokyo), pyrolysis of MSW in a quantity of 450 tonne per day. Pyrolysis products used as fuel in electricity generation.
|
[9] Wu C-H., Chang C-Y.,Tseng C-H. ‘Pyrolysis products of uncoated printing and writing paper on MSW’ Fuel 81 7119-7225 (2002)
|
Laboratory-scale pyrolysis of paper at temperatures up to ≈ 700°C. Calorific value of
the paper 12.5 MJ kg-1 dry basis. |
[10] Rovatti M., Converti A., Bisi M., Ferraiolo G. ‘Pryolysis of RDF: Kinetic modelling from product composition’ Journal of Hazardous Materials 36 19-33 (1994)
|
RDF in the form of fluff pyrolysed in small (24g) laboratory samples at temperatures up to 1000°C. Significant amounts of methane in the products.
|
[11] Chen K.S., Yeh R.Z. ‘Pyrolysis kinetics of epoxy resin in a nitrogen atmosphere’ Journal of Hazardous Materials 49 105-113 (1996)
|
Epoxy resin, as a component of MSW, studied for pyrolysis kinetics.
|
Reference [1] states that the gas yielded in the pyrolysis was comparable to town’s gas. ‘Town’s gas’ is a term having largely gone into obsolescence since reference [1] was published, but it means either gas from partial gasification of coal or gas from total gasification supplemented with some cracked hydrocarbon vapour (‘carburetted water gas’). Each has a calorific value of 20 MJ m-3. The fact that the gas in [1] had such a high calorific value must mean that considerable amounts of methane were present additionally to carbon monoxide and hydrogen, possibly also some ethane or ethylene. In the work summarised in the second row of the table the components showed the trend expressed in the shaded area below:
The work in reference [3] originates in Bangladesh, and its ultimate aim was to examine liquid pyrolysis products of paper waste for possible use with or in place of petroleum products in particular diesel. Yields of liquid of about 50% were obtained but with the very low calorific value of 13 MJ kg-1. This suggests that de-watering will be necessary before fuel use becomes viable. The water in the fuel might well have been not from moisture in the feedstock but product water resulting from breakdown of the cellulose. In the plant described in the following row, which originates in the Netherlands, steam is raised from combustion of the pyrolysis products and used to raise steam for power generation as explained.
Tetra Pak (row 5 of the table) products originate in Sweden and comprise a variety of food packaging materials adapted for particular applications and circumstances, for example long-term storage in a refrigerator. Low-density polyethylene, a common choice of material for the coating of paper, is present at about 20% in Tetra Pak products and it was found that on pyrolysis this gave a wax product. Polyethylene wax is of course a saleable substance although, of course, specifications apply according to the intended use. At pyrolysis temperatures of 600°C or higher the yield of wax from the polyethylene content of the Tetra Pak is quantitative.
In row six of the table pyrolysis of MSW in pelletised form, that is of RDF, features. The pellets were as low as 4% in moisture with the correspondingly high calorific value of 18 MJ kg-1. At a pyrolysis temperature of 700°C the gaseous product was about 25% carbon monoxide, 1% hydrogen and 5% methane, balance carbon dioxide. From calculations of the type which have been performed earlier in this book it is easily shown that such a gas would have a calorific value of just under 5 MJ m-3. At somewhat lower pyrolysis temperatures, up to 3% of C2 gases – ethane and ethylene – were formed also C3 and C4 gases in yields of about 1%. It is possible that these are not primary pyrolysis products but cracking products of the liquid pyrolysate. The liquids in fact had a calorific value of 35 MJ kg-1, a surprisingly high value auguring well for subsequent fuel use. The char residue for pyrolysis at 700°C had a BET surface area of over 200 m2g-1. For a carbon not ‘activated’ either by steam or with a chemical agent such as phosphoric acid this is a large surface area indicating promise of the product even without such activation as an adsorbent. Rows three and eight of the table are each concerned with studies of the paper component only of MSW, respectively in Bangladesh and in Taiwan. In row eight the calorific value of the paper in the work described has been noted because it is significantly below that of pure cellulose. This indicates the presence of an inorganic filler such as barium sulphate, a point which the authors of [9] have missed. That this could catalyse or in some other way influence pyrolysis behaviour is of course quite possible. At the highest of the pyrolysis temperatures in this study mass loss was about 75% or, equivalently, solid residue yield was about 25%. In some of the experiments levoglucosan C6H10O5 was identified in the pyrolysis products.
Epoxy compounds are ubiquitous and that some will find their way into the ‘city waste’ is inevitable. The work in the final row of the table is concerned with decomposition of an epoxy resin and Arrhenius parameters are determined. As would be expected these differ with extent of decomposition, and up to a fractional extent of 0.7 the value is in the range 150 to 170 kJ mol-1. This is a high value representing a pyrolysis rate very sensitive to temperature. The value of the pre-exponential factor ‘A’ of 1013 s-1 is also remarkably high for pyrolysis of an organic substance.
This section has been concerned with pyrolysis of MSW or particular components thereof and it will be followed by a discussion of pyrolysis of plastic wastes. Quite often MSW and plastic are blended for pyrolysis, and this will receive its due coverage at a later stage of the chapter.
6.3 Plastic waste
Polymer substances are of course made from petrochemicals and one expects abundant yields of hydrocarbons when they undergo pyrolysis. The approach taken in the previous section for MSW will be followed here for plastic waste: tabular presentation of information backed up with references and followed by comments.
Reference
|
Details
|
[12] Williams P.T., Williams E.A. ‘Recycling plastic waste by pyrolysis’ Journal of The Institute of Energy A71 81-93 (1998)
|
Polyethylene (PE), polypropylene (PP), polystyrene (PS), polyvinyl chloride (PVC) and polyethylene terephthalate (PET) pyrolysed in a laboratory-scale fluidised bed reactor at temperatures up to 700°C. When all of the plastics were pyrolysed together gaseous products included hydrogen, methane, ethane, ethene, propane, propene, butane and butene. Also some carbon monoxide. At the highest temperatures used an 88% gas yield. Wax/oil yields of up to 55% at the lower pyrolysis temperatures.
|
[13] http://www.xybernetizen.com/faq.html |
Chennai, India. Plastics excluding PVC and PS pyrolysed to give a preponderance of liquid product*.
|
[15] Lopez A., de Marco I., Caballero B.M., Laresgoiti M.F., Adrados A. ‘Pyrolysis of municipal plastic wastes: Influence of raw material composition’ Waste Management 30 620-627 (2010)
|
Plastic waste containing PE, PP, PS, PVC, PET and acrylonitrile butyl styrene (ABS) pyrolysed in 100 g samples. Liquid pyrolysate with calorific value up to 41 MJ kg-1 containing compounds in the range C6 to C21. Significant quantities of hydrocarbons in the gasoline carbon number range.
|
[16] http://www.wasterecycleplant.com/pyrolysis_fuel_system.html |
Pyrolysis of shredded plastic waste followed by cracking of the pyrolysate. Data examined for EROEI below.
|
[17] Demirbas A. ‘Pyrolysis of municipal plastic wastes for recovery of gasoline-range hydrocarbons’ Journal of Analytical and Applied Pyrolysis 72 97-102 (2004)
|
PE, PS and PP pyrolysed at temperatures up to 750°C with the intention of making gasoline. Yields of oil from PE and PP 40 to 50%. Yield from PS 25% plus major amounts of styrene monomer.
|
[18] Koo J-K ‘Reaction kinetic model for optimal pyrolysis of plastic waste mixtures’ Waste Management and Research 11 515-529 (1993)
|
Kinetic analysis of pyrolysis of mixtures of PE and PS.
|
[19] Zevenhoven R., Axelsen E.P., Hupa M. ‘Pyrolysis of waste-derived fuel mixtures containing PVC’ Fuel 81 507-510 (2002)
|
Pyrolysis of PVC in 10g quantities at temperatures up to 1100°C.
|
[20] Ma S., Lu J., Gao J. ‘Study of the low-temperature pyrolysis of PVC’ Energy and Fuels 16 338-342 (2002)
|
Pyrolysis of PVC.
|
In reference [12] (row one) the plastics identified were pyrolysed both individually and all together. In the latter case the yield of gas at about 700°C was remarkably high, and the gas would have had a calorific value on a volume basis higher than that of natural gas let alone that of the producer gas. The potential for fuel use of the gas is clear but there are important questions to be addressed first. Containing several hydrocarbons in the C2→4 range, the gas would not be suitable for use on a burner designed and adjusted for natural gas. Indeed, serious accidents have resulted when LPG (C3 and/or C4) has been substituted for natural gas on a burner designed expressly for the latter. The reason is that methane, being C1, is the least reactive alkane. Ethane (C2H6), propane (C3H8) and butane (C4H10) have higher reactivities than methane and therefore higher flame speeds. The expected result when a mixture of these is substituted in ignorance for natural gas is burner flashback. A high-BTU gas produced by pyrolysis becomes a less attractive resource if its use involves burner adjustment or even replacement. Possibly such a gas, if available in small but steady and reliable supply, would on a burner designed and tested for the gas be suitable for use in an application such as flame cutting in which usage is intermittent and amounts of fuel gas used are not huge.
The plant at Chennai (second row) was made by Polymer EnergyTM in the US, which has a number of installations in the East including one in Thailand [14]. It produces 750 to 800 litres of oil per tonne of waste processed and this is seen as having refining potential. It is interesting to note that PS is not accepted at the plant, and the reason on reflection is fairly obvious. The empirical formula of styrene monomer is CH, and the low hydrogen-to-carbon ratio will make for a low extent of pyrolysis to gaseous products and large amounts of char and/or organic sludge. As well as not being the desired product, these adhere to surfaces within the reactor and necessitate more frequent cleaning than would otherwise be the case. The empirical formula of ethylene monomer is CH2, and the plant at Chennai accepts polyethylene ‘within certain limits’ [13]. PP – monomer empirical formula C3H8 or in effect CH2.7 – is accepted unconditionally at the plant.
To the information in row three will be added the following. The gaseous pyrolysate has calorific values of 47 MJ m-3 indicating a preponderance of C2+ gases. The solid residue the organic composition of which will approximate to pure carbon has quite low calorific values, only up to 17 MJ kg-1. This is of course due to the presence of such materials as glass and these residues would not be suitable for direct combustion because of the quantity and nature of the ash which the combustion would generate. Gasification would be possible but here again the high ash would work against viability. If the char were steam activated or chemically activated to make an adsorbent it might function well enough as such, but a common eventual fate of adsorbents is incineration so even this application is precluded by the ash and the solid is the least attractive of the three classes of pyrolysate from the study in [15].
In reference [16], pyrolysis followed by cracking of the product, pyrolysis gas is burnt to provide heat for cracking and this need not feature in an EROEI calculation which, it must be remembered, is in no sense an energy balance. It is stated in [16] that 8 m3 per day of liquid in the gasoline and diesel boiling ranges is produced and that heat for the pyrolysis is provided electrically with a daily consumption of 500 kW hour. These data are examined in the boxed area below.
The EROEI calculated would exceed that for any crude oil in this early 21st Century, but 150 would in fact have been a typical value about 60 years ago when offshore oil and gas production were just beginning in the Gulf of Mexico using wells which by today’s standards were very shallow. So there is no reason why the EROEI calculated above cannot be at least cautiously accepted and it augurs well for the production of liquid fuels by the treatment of plastic waste described in [16]. Of course, there would be quality issues to be addressed were the liquids to find automotive use. The same would be so were the mixture of pyrolysis oils and styrene monomer referred to in the next row to be used as fuel for a spark ignition engine. The styrene would enhance the octane number, but whether such a mixture would be suitable for use in viscosity and vapour pressure terms would need close attention.
The kinetic modelling work referred to in the antepenultimate row of the table led to the conclusions that the most influential factors in determining the distribution of products are temperature and weight ratio of the two polymers co-pyrolysed. If oil is the desired product a temperature of 600°C is most suitable. Interestingly, the analysis predicts that other things being equal a PE-PS mixture decomposes to oil more rapidly than PE alone. PVC pyrolysis features in the next row, and it is widely known that this leads to hydrogen chloride and char in a process known as ‘dehydrochlorination’. In [19] it was observed that this process began at 250°C and that at 350°C the PVC had lost 99.5% of its chlorine content. This means negligible chlorine in the char residue, which was found to have a calorific value as high as 38 MJ kg-1. This indicates significant hydrogen in the char, and a simple calculation is possible to show this. Vinyl chloride monomer having undergone ‘dehydrochlorination’ consists of a fragment C2H2 having:
(2/26) × 100% = 8% hydrogen to the nearest whole number.
At 350°C the char remaining after hydrogen chloride release will not dehydrogenate to a major extent, though it will at the higher temperatures used in the work under discussion. A value of 8% is an unusually high one for a char, and the calorific value of the char is higher than that of elemental carbon. This is due to the high hydrogen content of the char. Reference [20] (final row of the table), also concerned with PVC pyrolysis, confirms that beyond the limit of dehydrochlorination at about 300°C there is hydrocarbon gas production, and this will of course reduce the hydrogen content of the residue to a value more typical of a char.
It is fairly clear that some control over pyrolysis product nature and distribution is achievable by adjustment of reacting conditions. Similarly co-pyrolysis – that is, pyrolysis of two substances as a mixture - can be used to give a good yield of desired product and there might be other good reasons for co-pyrolysis including concurrent treatment of municipal and trade waste. In the first part of this chapter biomass pyrolysis was discussed with special emphasis on co-pyrolysis with some other type of waste. Consequently some examples of co-pyrolysis will be studied in the next section.
6.4 Co-pyrolysis
One obvious point is that to co-pyrolyse biomass with plastic in some degree mitigates the non carbon neutrality of the latter, giving any pyrolysate product for subsequent fuel use a degree of carbon neutrality which can be estimated and factored into carbon accounting. This is analogous to coal-biomass co-firing in combustion. A hot-off-the-press report [21]([21] Brebu M., Ucar S., Vasile C., Yanik J. ‘Co-pyrolysis of pine cone with synthetic polymers’ Fuel –in press.) originating from Romania describes co-pyrolysis of PE, PP and PS with a form of biomass locally available in abundance, namely pine cones (Pc). These were copyrolysed at 500°C. Pc and PE in a weight ratio of 1:1 gave a product distribution gas 15.9%, liquids (total, aqueous + organic) 47.5% and char 36.6% Results were not widely different with Pc and PP; however, the trend noted above whereby PS gives on pyrolysis very limited gas was found in [21], and Pc and PS in equal quantities gave only 8.8% of gas. There was detailed analysis by GC-MS of products and the compounds in the aqueous phase were diverse. With Pc and either PE or PP or PS the aqueous pyrolysate had up to 10% of carboxylic acids up to C3, acetic acid being the most prevalent. With the various Pc plastic mixtures studied the tar/oil component of the products contained compounds up to about C26 with calorific values sometimes as high as 46 MJ kg-1. Chars had calorific values up to about 35 MJ kg-1; a bituminous coal with this calorific value would be expected to attract a good price!
Co-pyrolysis of biomass with coal is also of increasing importance, and here again a degree of carbon neutrality is introduced by inclusion of the biomass. In a fairly recent experimental study [22]([22] Zhang L., Xu S., Zhao W., Liu S. ‘Co-pyrolysis of biomass and coal in a free fall reactor’ Fuel 86 353-359 (2007)) of coalbiomass co-pyrolysis the coal was a low-rank one, actually a lignite originating in China given in [22] the abbreviation DY. This was co-pyrolysed with legume straw (LS) at temperatures in the range 500 to 700°C. Across the temperature range an increase in the LS:DY ratio led to a decrease in char yield as would be expected and an increase in gas yield; liquid yield was not very strongly affected. A high LS:DY ratio raised oxide of carbon yields in the gaseous pyrolysate and had the same effect on hydrogen yields. If fuel utilisation of the gas was intended, carbon monoxide and hydrogen would be the most desired products. Methane, having a much higher calorific value molar basis than either hydrogen or carbon monoxide, is a significant bonus in such a pyrolysate gas even at low levels. It occurred at about 2% level in the work under discussion.
Oil is of course obtained from shale by pyrolysis of the kerogen within the shale leading, probably after desulphurisation and hydrogenation, to syncrude. The idea of including plastic waste with shale for pyrolysis is an interesting one and has been examined in work including that described in [23]([23] Ballice L., Yuksel M., aglam M., Reimert R., Schulz H. ‘Classification of volatile products evolved during temperature-programmed co-pyrolysis of Turkish oil shales with low density polyethyene’ Fuel 77 1431-1441 (1998)). In this work shales from two sources were pyrolysed with and without low-density polyethylene (LDPE) at temperatures up to 500°C and effects of the LDPE assessed. Not only amounts of products but also their distribution was affected by the LDPE, and the yields of products is particular carbon number ranges was controllable by means of the dual factors of temperature and kerogen:LPDE ratio. Reference [23] was published in 1998 and a question which has crossed the present author’s mind would almost certainly not have been raised in 1998. Wherever there are attempts to make oil from shale the EROEI is of paramount importance. Is there potential to raise the EROEI by co-pyrolysis of the kerogen with plastic? Oil from shale usually operates on a slender EROEI and is therefore vulnerable if there is a downward movement of conventional oil prices. We might expect to see more of the type of work described in [23] as efforts are intensified to produce oil from shale, for example in parts of the US including Colorado.
6.5 Concluding remarks
The scope for production of organic chemicals from pyrolysis of waste is very wide indeed. Gaseous pyrolysate can always be used as a fuel gas or as a synthesis gas. Liquid pyrolysate can always be used as a liquid fuel. Solid residue can always be used as a solid fuel or to make products such as adsorbent carbons. The challenge is in making use of the pyrolysis products viable under circumstances such that they are produced ‘here and there’ without any national (let alone international) network or distribution structure and are in competition with conventional fuels with extensive capitalisation in distribution infrastructure.
next Examples of Gasification of Wastes
No comments:
Post a Comment
Please wait for approval of your comment .......