previous VENTURI TUBES


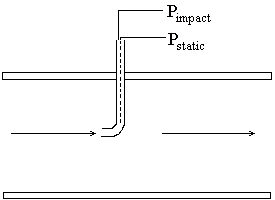

Pitot tubes are used to q easure the flow of gas, steam, water, and other liquids in ducts and pipes. A pitot tube is a device that consists of a tube having a short , right-angled bend that is placed vertically in a moving body of fluid with the mouth of the bend directed upstream (figures 5-12 through 5-16). The most common applications include heating, ventilating, and air-conditioning (HVAC) systems and low velocity drafts. Pitot tubes are widely used as permanent and spot-check meters. Their characteristics are well known and information is widely available. Pitot tubes are generally less than l/2-inch in diameter and are inserted into the flow stream at right angles to the flow. Pitot tube meters measure the velocity of flow at only one point. If properly installed, they provide accurate and reliable flow measurement. Pitot tubes are suited for low to medium flow in large ducts. Due to their small size, pitot tubes cause very little permanent pressure loss. They are excellent for monitoring purposes because they are so portable and easily inserted and withdrawn from a flow stream.
1. Operating Principle: The principle used in a pitot tube meter is that when a flowing fluid impacts an object, its velocity drops to zero and the pressure at impact increases. The pitot tube measures the difference between impact (velocity) pressure and static pressure created at impact. Flow rate is determined by comparing the two pressures and the known relationship between pressure and flow rate.
METER DESIGNS: Differences in pitot tube designs are in the positioning of static and dynamic pressure taps that are used in measuring pressures and whether the installation is to be permanent or for temporary spot monitoring. Some designs place the taps separately, with the static tap located at the duct wall and the impact tap at the end of the pitot tube (Figure 5-12). Other designs locate both taps on the tube. A single point pitot tube infers the flow from single position readings.
Averaging pitot tubes have more than one impact hole along the leading edge of the tube (Figure 5-13). The static tap is generally placed on the downstream side of the tube. The tube is screw-fitted into place. The multiple impact holes provide for an averaging of the velocity across the pipe instead of at a single point. Cylindrical-bodied averaging pitot tube meters have proven to be nonlinear (and nonrepeatable) over most of the flow range. Only designs that incorporate some sort of vortex shedding body should be used. Both permanent and portable units can be used to measure flow rates of gases, air, and steam. The pitot tube is especially useful in odd-shaped or large ducting.
RECOMMENDED APPLICATIONS: Pitot tube meters are appropriate for measuring gas and steam flow in round pipes with diameters greater than 3 inches, especially when venturi tubes and orifice plates are too expensive to utilize or cause too great a permanent pressure drop. A pitot tube is recommended where developed flow is possible by assuring minimum straight lengths of pipe upstream and downstream of the tube. Permanent mountings are particularly attractive when repeated readings will be made but other meters are too expensive.
FIGURE 5-12. Pitot Tube Meter
FIGURE 5-13. Averaging Pitot Tube
FIGURE 5-14. Single Hole Pitot Tube With Separate Static Tap
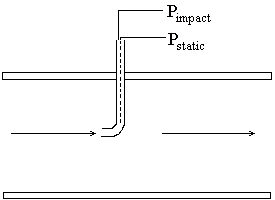
FIGURE 5-15. Hemispherical Head Pitot Tube
FIGURE 5-16. Commercial Pitot Tube
LIMITATIONS: The use of a pitot tube meter at a specific location may be limited by the following requirements:
- Only clean fluids can be measured.
- A recommended minimum length of straight pipe is required.
- Meter is susceptible to errors when metering an undeveloped or disrupted flow profile.
- Temperature is limited to 537°C (1,000°F).
- Pressure limit is 6,000 psig.
- Turndown is limited to approximately 3:1. (Range can be increased by stacking dp transmitters.)
INSTALLATION: Figures 5-13 through 5-16 illustrate a variety of pitot tube installations. The static pressure tap can be located either on the pipe or duct or be incorporated in the pitot tube itself. The pitot tube is inserted at right angles to the flow. The impact port must meet the flow squarely. Placement of the tube is critical. The pitot tube measures velocity at only one point. The single point is used to calculate average flow velocity, but does not necessarily represent average velocity (vcritical). In small lines, it may be impossible to place the pitot tube at ‘critical because of the pipe wall. It may be necessary to q easure flow at multiple locations to establish a relationship between the final pitot tube location and the actual flow. It is preferable to locate the pitot tube in a horizontal line. To ensure accurate flow measurement, the fluid MUST enter the pitot tube with a fully-developed velocity profile, free from swirls or vortices. Such a condition is best achieved by the use of adequate lengths of straight pipe, both preceding and following the pitot tube. The minimum recommended length of upstream piping is 7.5 times the pipe diameter. For specific lengths for a particular installation, consult manufacturer. The length is necessary to limit errors, due to piping configurations, to less than ±%0.5 percent. If minimum distances are not observed, the pitot tube meter may produce inaccurate data. In ducts that do not meet straight length requirements, it is necessary to take multiple samples to obtain an adequate flow profile.
1. Permanent Mounting With Separate Static Tap: In this option, the pitot tube impact tap is permanently mounted facing directly upstream. It is located at a point where the velocity measured represents average velocity. The static tap is drilled through the wall of the pipe less than one-half pipe diameter upstream of the impact tap. Both taps are for screw-fitted components.
MAINTENANCE: The following procedures are the minimum required for the most common types of units. When developing maintenance schedules, refer to the manufacturer’s instructions. To ensure reliable flow data, the following actions must be undertaken quarterly or when data accuracy is suspect:
- Check for clogged orifices.
- Check tip for wear.
- Sensor lines should be blown down on a regular schedule.
- Rescale dp transmitter if necessary, based on flow of previous year.
- Test dp transmitter with dead weight pressure tester and rescale if necessary.
ACCURACY AND RELIABILITY: Accuracy is typically ±%5.0 percent of full scale. For specific applications, accuracy can be up to ±%0.75. Pitot tubes are reliable as long as the fluid being measured is sufficiently clean to avoid clogging the orifices. With contaminated or dirty fluids, Increased maintenance may be necessary to ensure accuracy.
Nice blog great information...
ReplyDeleteThanks for sharing...
Flow Meter, Humidity Meter, Countroller, Temperature Controller